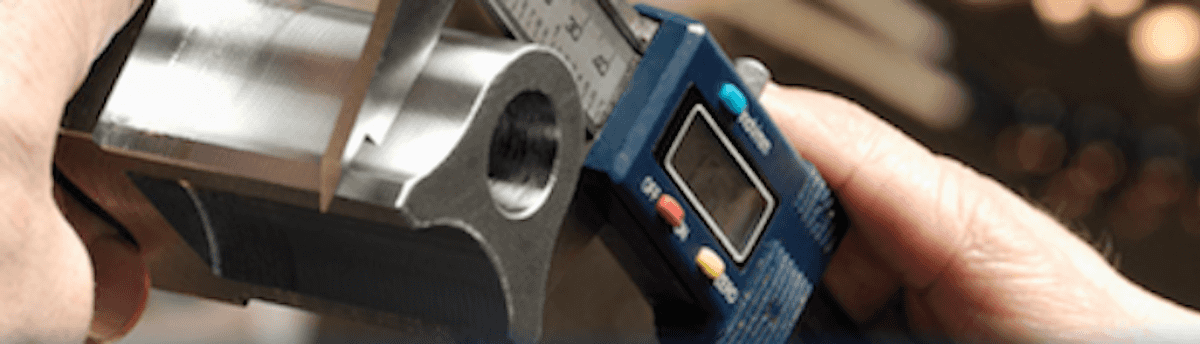
Quality
Compass Precision’s mission, from first prototype or initial production delivery through end of program, is to exceed our customers’ expectations for quality. This means all dimensions and properties must be well within spec, all paperwork and certs complete and accurate, all surface finishes meeting expectations, and no surprises when parts arrive.
We take this mission seriously.
We believe excellence in quality starts with a commitment to fully understand our customers’ requirements and needs, including those unwritten and unspoken. Our people take the time necessary to recognize and comprehend all drawings, solid models, and other specifications.
If we don’t understand something, we ask before order is placed. If we have suggestions that may positively impact part quality or cost, we offer them, again before order is placed.
Our manufacturing and quality assurance teams have significant experience and consistently get top marks on customer scorecards. They utilize in-house quality control procedures to ensure total compliance with all specifications to each customer.
Our gage blocks, surface plates, instruments, and inspection equipment are calibrated and traceable. We utilize a variety of dimensional inspection methods to verify the accuracy of part features, including, where appropriate, coordinate measurement machines that automate and support dimensional inspection.
And if we need something to support the inspection of a new part, we get it – period.
We may lose an order due to price, and occasionally because our lead-time is too long, but NEVER because we compromise on quality.
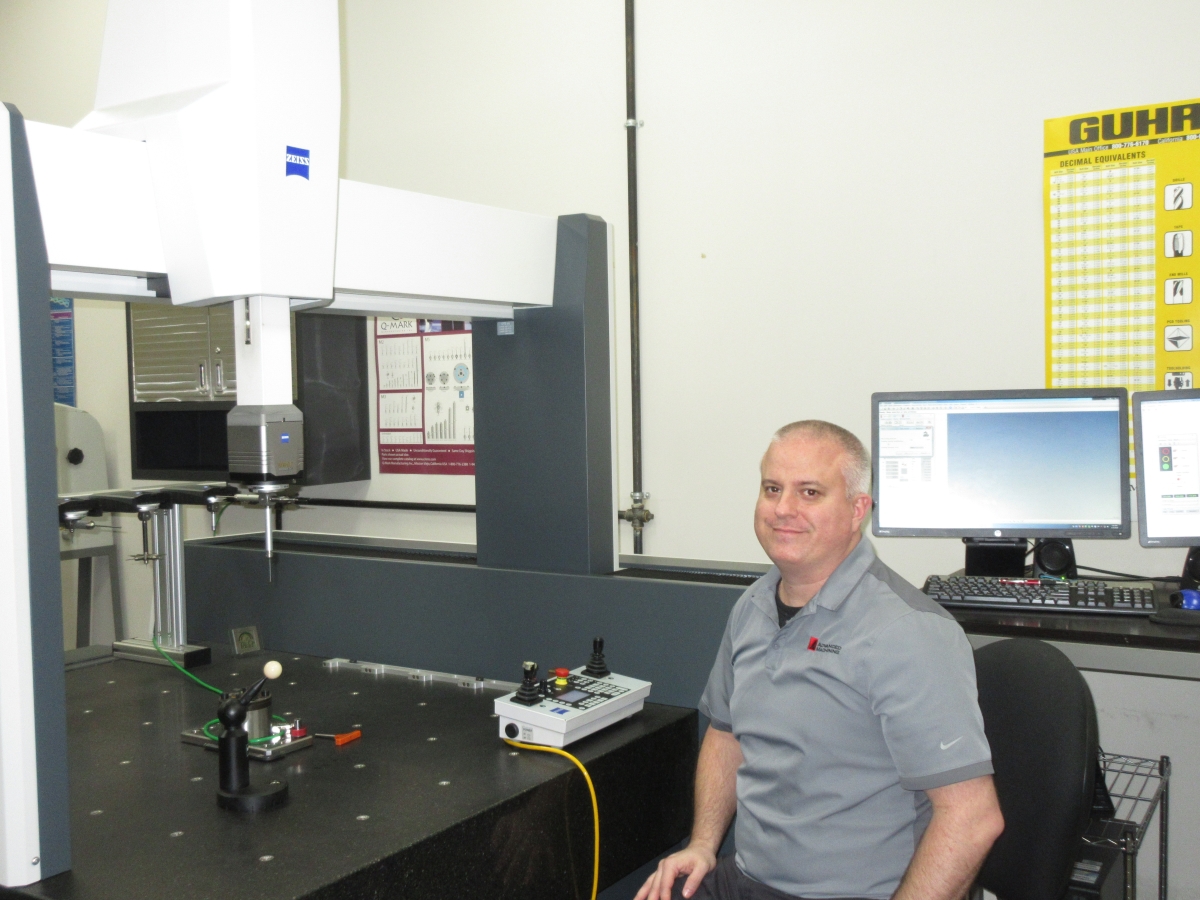
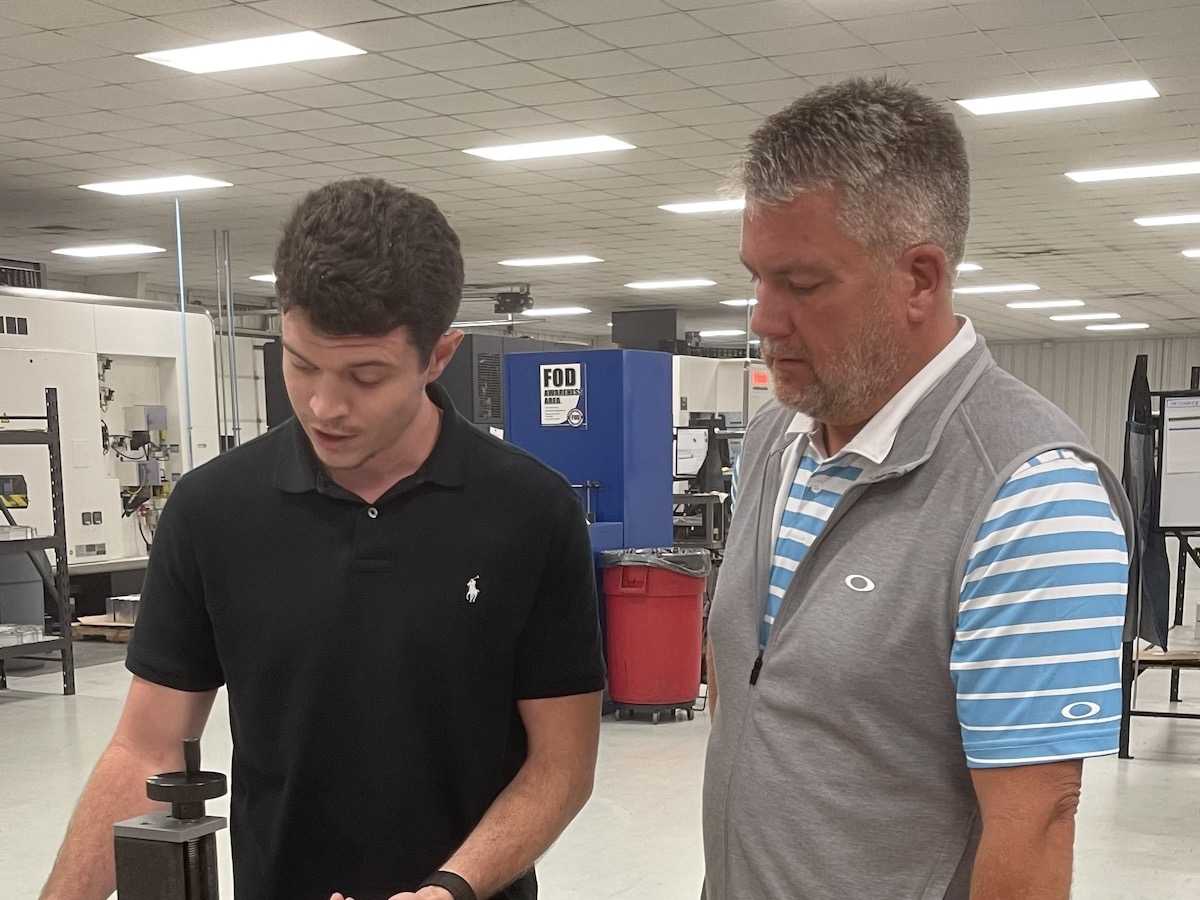
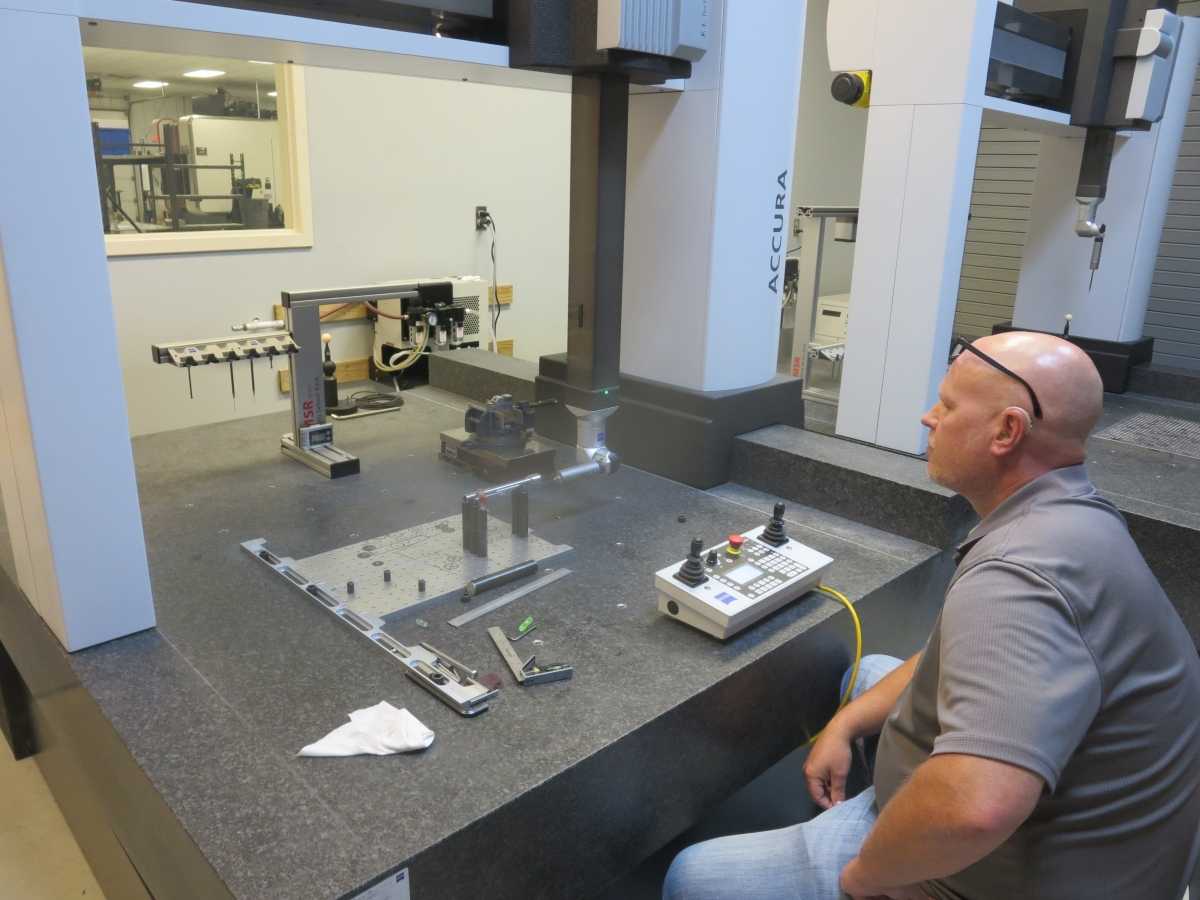
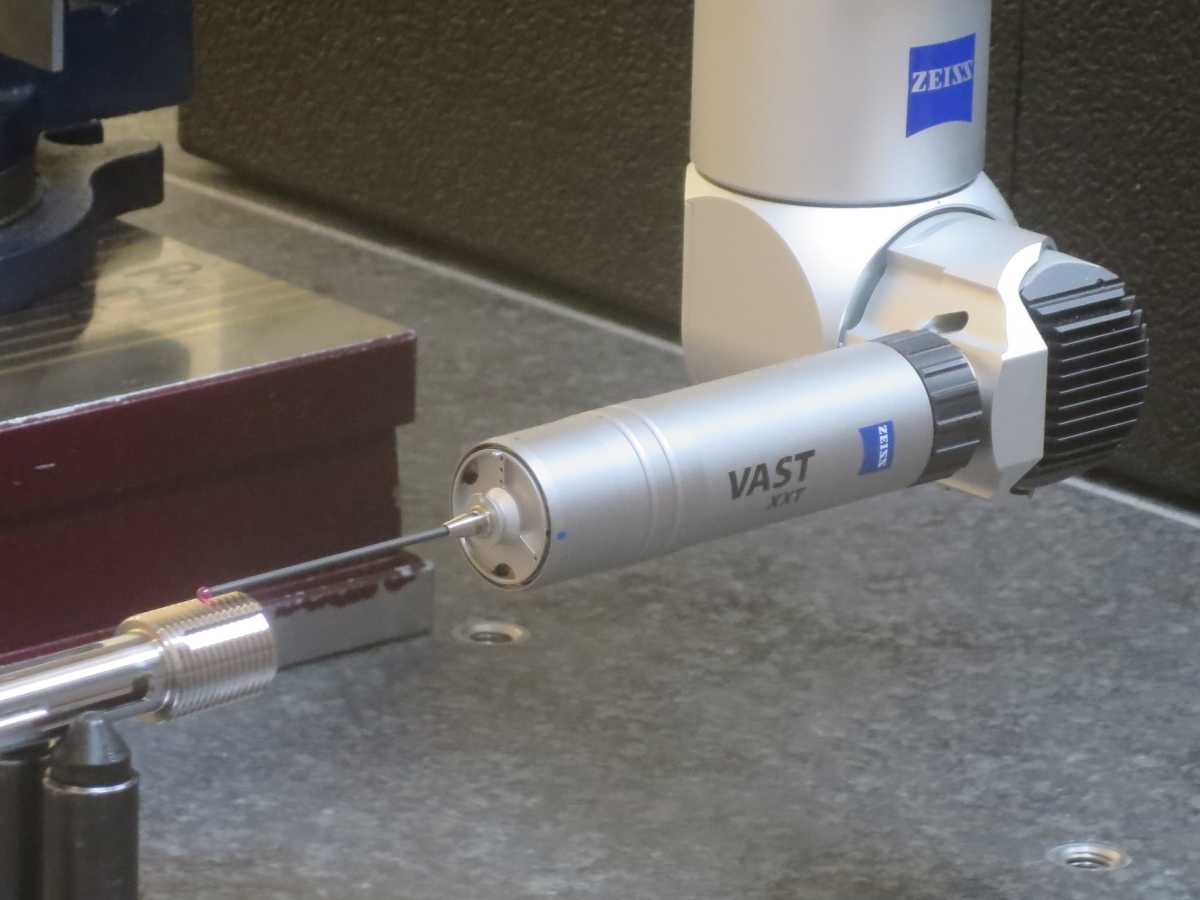