Successfully Fabricates Parts from Unknown Material
Charlotte, NC – November 12 – Overcoming insurmountable odds and fast tracking a new part is nothing new to Compass Precision and its shops. This month, Quality Products & Machine is literally bending its capabilities to complete the delivery of a recent purchase order.
A leading manufacturer of CNC machined and fabricated metal components, Quality Products recently received an order from a major aerospace and space customer for a brand new part. The order was set to test the capabilities of the Compass operating company.
Quality passed the test and then some (see Quality Products’ Don Bartlett holding finished part in pictures above and below).
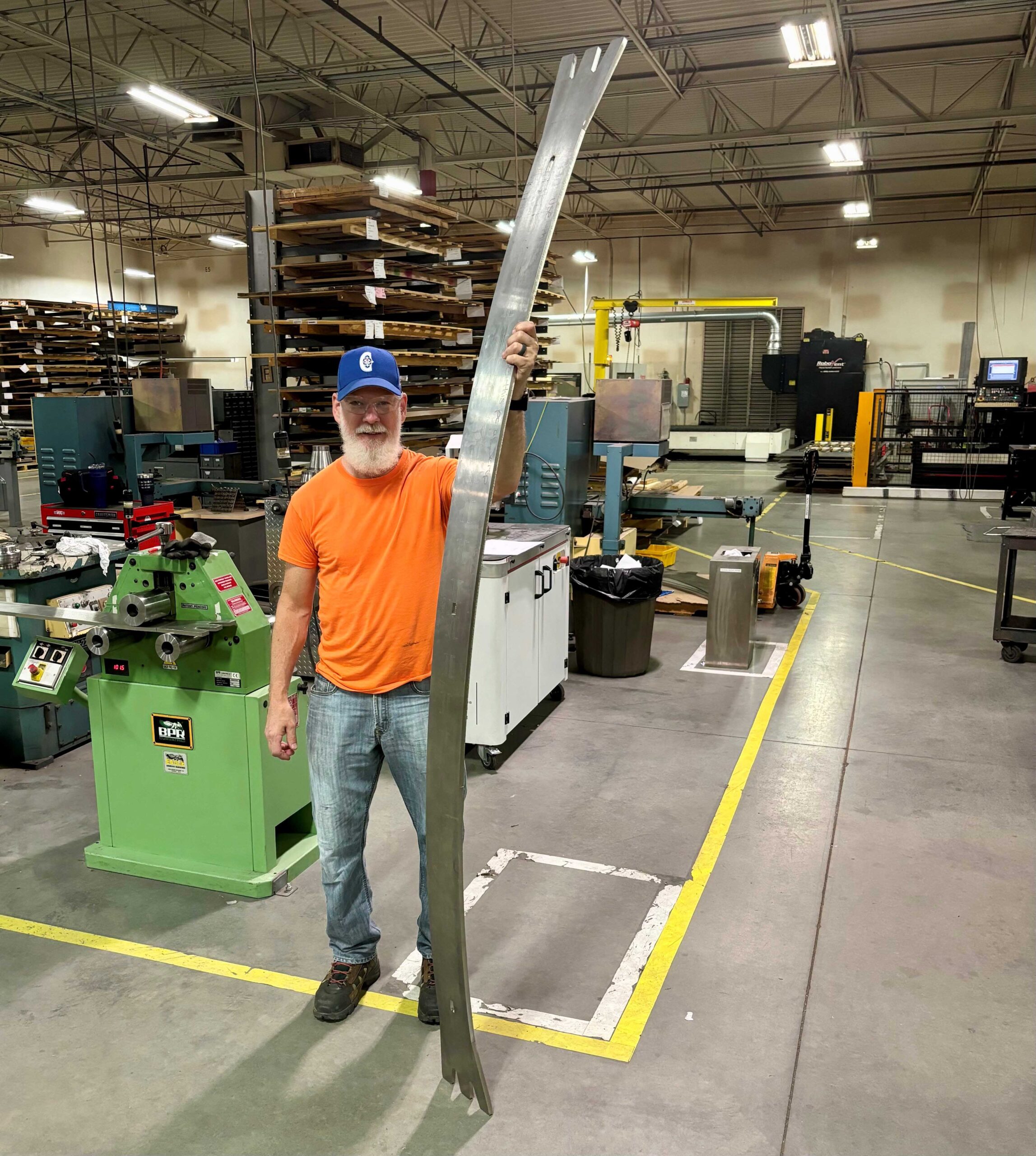
”I almost couldn’t believe my eyes when I saw the drawing,” exclaimed Jim Miller, Compass VP of Sales. “The customer wanted a nearly ten foot part, with precise holes and features machined in, then the whole thing bent to create an arc of constant radius.”
“But the craziest thing is that they provided the material but wouldn’t tell us what it was. We had absolutely no idea about the material’s properties or chemistry.”
“If there ever was a situation that required working blind,” added Compass VP & COO Bill Canning. “This was it.”
Some of Quality’s sister companies at Compass have previously worked with the aerospace and space customer. But searching for a machine shop with both machining and fabrication to complete its latest project, the customer chose to work with Quality after receiving that recommendation from Jim
A fab and machine shop, Quality was a natural choice. But the new part was going to be the biggest ever made at the Compass operating company. The material the part was to be made of was also confidential, so Quality wouldn’t be able to conduct any research to find previous best methods to work with the material.
“It kind of pushed our capabilities a little bit. Because previously, we only used to roll anywhere up to a quarter-inch thick and maybe 3 inches wide,” Quality Products Vice President and General Manager Dustin Jones said. “But this one is half-inch thick and 6-7 inches wide.
“It’s also a pretty nasty alloy that our customer developed itself. It’s unique because the colder it gets, the tougher that material gets.
“It’s one of the thickest parts we’ve cut on the laser. It took some development to get it laser cut right. Originally, we didn’t know if we could actually roll it. We had to rebuild the machine, do some different dies, and iron out the process on that. It was a lot of trial and error.”
Dustin described that, at first, the Quality Products team was hesitant that the company could meet the customer’s demands. But with the proper adjustments, they fulfilled an order of 36 parts.
“With the die setup [we had], it was requiring more tonnage than what that machine could handle. So we were out of the capability range of that machine. So we came back, utilized Solidworks, did some quick math, adjusted and made new dies,” said Dustin.
“The new dies reduced the tonnage required to roll the part. And then from there, we were able to gradually go. We had to reduce the amount of bending we did per run. Then, we just kind of work it in.”
Thanks to completing the first order, the customer notified Quality Products that it would be placing more orders for the part in 2025.
In response, Compass did what it often does to satisfy a customer – the parent company bought new equipment for Quality Products to make the process more efficient. A new bigger roller arrived at Quality Products and was installed on Nov. 6.
The operating company has already begun using the bigger roller on the new order. Dustin said the new roller has stabilized the process so that the same exact bend can be made every time.
The first order Quality received for the part took more than a week to complete. Going forward, it will take one day.
”This project epitomizes what Quality Products is all about,” explained Bill. “We stretch our capabilities, figure out what needs to be done, then invest in new equipment to do it better.”
The success story has pleased the aerospace and space customer so much, they have placed other orders for new parts to utilize Quality’s new roller.
”I have always said that Compass and its shops seek to do the tough stuff, the most difficult projects,” said CEO Gary Holcomb. “Dustin and his band of overachievers at Quality Products certainly did that with this part.